HRSflow AUTOMOTIVE TECH DAY
Melt Management Solutions For Class “A” Surface Finish.
Dimensional Stability and Family Molds.
Live Demonstrations • Best Practices • Networking Opportunity
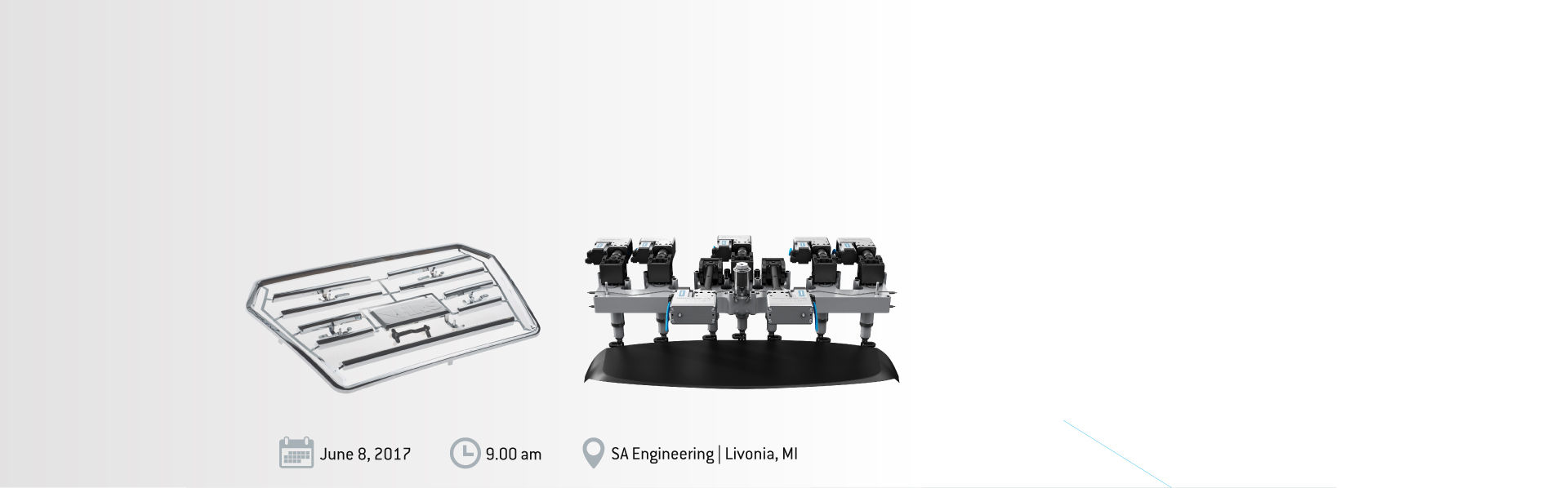
ABOUT THE EVENT
A 360-degree view of the Injection Molding Process with executive professionals of the plastics industry.

AGENDA
> 9.00 am Registration & Networking
> 9.45 am Welcome to the Automotive Tech Day - HRSflow & SA Engineering
_______________________________________________________________
> 10.00 am Expanding Process Capabilities with FLEXflow, Stephan Berz, HRSflow Vice President Sales
> 10.30 am Innovative Polypropylene Compounds Replacing Engineering Plastics and Metals, Neil Fuenmayor, LyondellBasell Automotive Market Development Manager - North America
> 11.00 am Coffee Break
> 11.15 am DecoJect® - A Cost Effective and Flexible Way to Produce High Class Interior Elements, Joachim Kragl, ENGEL Director of Advanced Molding Systems and Processing - North America
> 11.45 am Inmolt: Integrated Primering, William Asmann, Nolax, Inc.North American Account Manager
> 12.15 pm Lunch
________________________________________________________________
> 1.30 pm FLEXflow Live Molding Demonstrations: Front Chrome Grille and Spoiler Molds
> 3.30 pm Summary of the day's events - Q&A
> 4.00 pm Refreshments & Networking
THE SPEAKERS
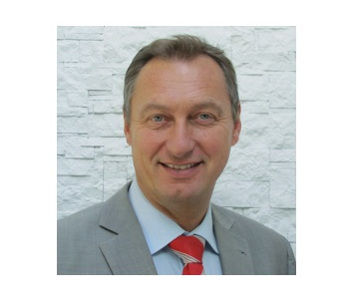
STEPHAN BERZ, HRSflow Vice President Sales
Expanding Process Capabilities with FLEXflow
The presentation will explore the main benefits of FLEXflow Technology: the servo driven valve gate system that assures accurate, easy to operate and flexible control of pressures and flow rates in a precise method. Mr. Berz's presentation will analyze a case study of 2 exterior applications where the FLEXflow System provides a wider process window during the injection molding process. Using FLEXflow Technology demonstrates this innovative solution is capable to provide class "A" plated mold parts in a single shot, using a "family" mold. This is truly "A First" in injection molding processing.
About Stephan Berz: Vice President of the Italian hot runner specialist HRSflow and Automotive Sales Director, he is responsible for global sales activities in the automotive sector. He has studied plastics engineering and has worked for many years in senior positions in the plastics industry.
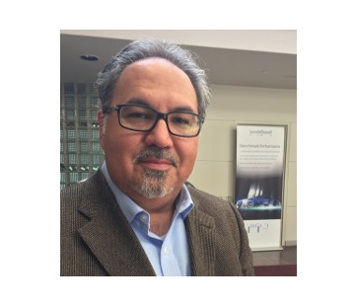
NEIL FUENMAYOR, LyondellBasell Automotive Market Development Manager
- North America
Innovative Polypropylene Compounds Replacing Engineering Plastics and Metals
LyondellBasell has been driving innovation with new polypropylene compounds offering high performance property profiles for automotive applications that have traditionally used engineering thermoplastics and metals. These advanced polypropylene compounds, featured in LyondellBasell’s global “Save10” innovation portfolio, are now successfully being used for body panels, roof spoilers, liftgate panels, structural parts and underhood components. Aided by the low density that polypropylene offers, as well as unique advancements in reinforcements and formulations, these materials demonstrate improved performance, weight savings, cost savings and better processability over engineering resins and even metals.
About Neil Fuenmayor: at LyondellBasell, the world’s leader in polyolefins, Neil is the North American Automotive Market Development Manager, responsible for all OEM efforts and leads a growing team of 7 dedicated OEM aligned market development managers.
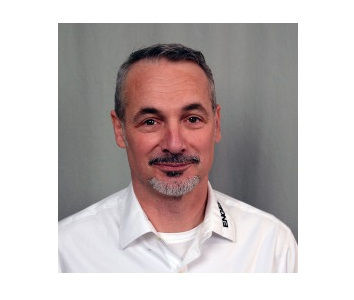
JOACHIM KRAGL, ENGEL Director of Advanced Molding Systems and Processing - North America
DecoJect® - A cost effective and flexible way to produce high class interior elements
Molding and designing in one step: The combination of injection molding with IMG (in-mold graining), straight from the roll to the mold. In contrast to the conventional IMD process, DecoJect® does not simply transfer the paint from the foil to the component, but rather the foil is punched out and remains on the component. In addition to color and pattern, this also allows for the application of surface structures to the foil. The result is a significant cost advantage over conventional technologies for the production of premium visible components. The efficiency potential is especially high with respect to the harmonization of interior components consisting of different base materials.
About Joachim Kragl: he graduated from the TGM College for Polymer Engineering and Processing and he began working as an applications engineer in the processing department of ENGEL Austria. He assumed his current role as director of advanced molding systems and processing for ENGEL North America in July 2009.
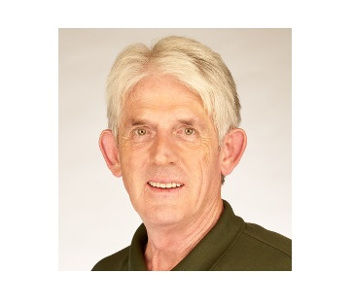
WILLIAM ASMANN, Nolax, Inc. North America Account Manager
Inmolt: Integrated Primering
During the injection molding process, Inmolt transforms the non-polar surface of PP into a polar one. The finished parts can then be directly foamed, printed, laminated, or lacquered. Inmolt simplifies the production of polar PP parts by eliminating the pretreatment process.
About William Asmann: after spending several years with major UV systems manufacturers in product development, engineering and management positions, since 2003 he is working for Nolax, an adhesives think tank with headquarters in Switzerland.
FLEXflow LIVE MOLDING DEMONSTRATIONS
Are you ready to experience our FLEXflow Technology for automotive premium parts?
The innovative, servo-driven valve gate system for accurate, easy to operate and flexible control of pressures and flow rates.
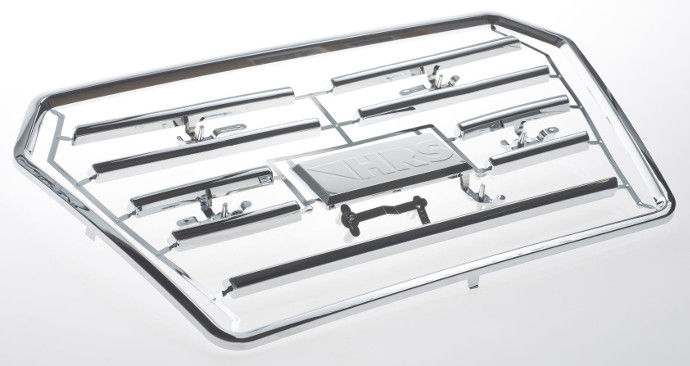
FRONT CHROME PLATED GRILLE
Main Benefits
Breakthrough technology for family molds
Achievable superior surface quality results
Molded parts to chrome-plated without additional preparation
Technical Features
- Live molding demonstration on 600 - ton ENGEL IMM
- Nominal part dimensions: 22.8 x 13.0 in (580 x 330 mm)
- Nominal part weight: 297 g
- Nominal part thickness: different wall thickness, from 0.08 to 0.12 in (from 2 to 3 mm)
- System Type: 10 Conical Valve Gate Ma series
- Cascade system: 10 FLEXflow drops, servo driven valve gate
- Molding material: PC/ABS
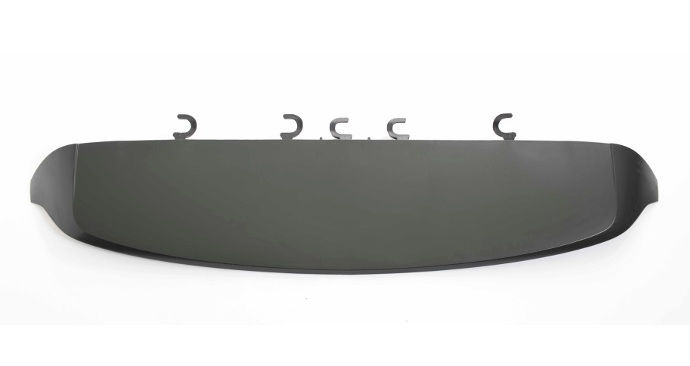
AUTOMOTIVE SPOILER
Main Benefits
Suitable for automotive large-format parts
Superior solution for demanding aesthetics in surface applications
Optimal flow and pressure distribution during processing
Technical Features
- Live molding demonstration on 1000- ton ENGEL IMM
- Nominal part dimensions: 49.6 x 11.0 x 4.7 in (1260 x 280 x 120 mm)
- Nominal part weight: 1010 g
- Nominal part thickness: 0.12 in (3 mm)
- System Type: 5 Conical Valve Gate G series
- Cascade system: 5 FLEXflow drops, servo driven valve gate
- Molding material: PP/EPDM 20% Talc
CONTACT
Location
SA Engineering
38103 Schoolcraft Road
Livonia - MI 48150
Email
Our events staff
are at your disposal:
events@hrsflow.com
Telephone
For any questions please contact:
+1 616 228 6906 Sara Wildfong
+1 616 228 6905 Christina Hunting
Accommodations
We recommend the Comfort Inn Hotel Livonia: 29235 Buckingham Ave., Livonia, MI 48154 Ph. +1 734 458 7111
Reserve your place for HRSflow Tech day:
Limited seating available!