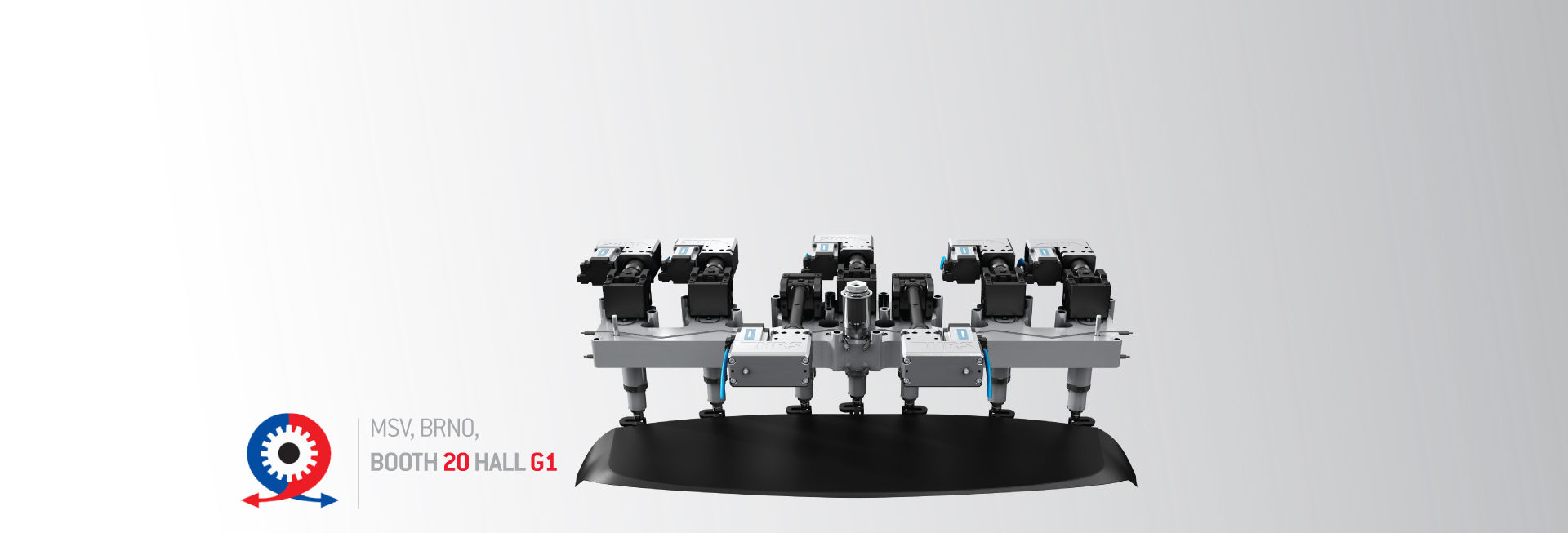
FLEXflow CHALLENGING APPLICATIONS AT MSV 2018:
Visit our booth and see with your own eyes the benefits of our servo driven valve gate technology.
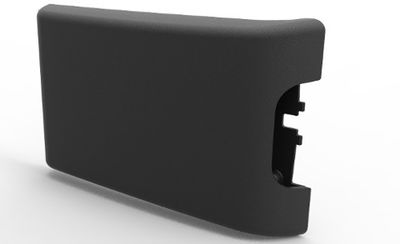
Technology for next generation lightweight vehicles
Application: lightweight center console armrest
Material: PP, TPV
Hot runner system: (2+3)FLEXflow drops, servo driven valve gate
In cooperation with: Krauss Maffei, HRSflow, Proper Tooling
Special features: FLEXflow, TPV overmolding, lightweighting.
The load-bearing structure is created from a thin-walled, fiber-reinforced organosheet, using the FiberForm process developed by KraussMaffei. First of all, this is over-molded with polypropylene (PP) and finally with a thermoplastic elastomer (TPV), whereby a soft, finely grained visual surface is formed.
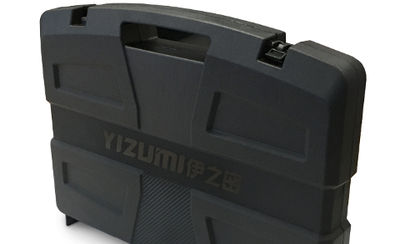
Premium technical parts
Application: tool case, technical
Material: PP 18% talc
Hot runner system: 3FLEXflow drops, servo driven valve gate
In cooperation with: GK (Georg Kauffmann), HRSflow, Lyondellbasell, Yizumi
Special features: FLEXflow, MuCell®, lightweighting
Its production is based on the FoamPro foaming process from development partner Yizumi, and a FLEXflow triple-nozzle hot runner system from HRSflow with back-injection. The finished part is characterized by a high-quality, finely structured surface.
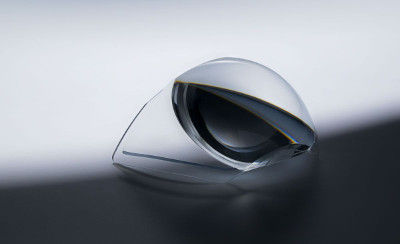
Thick walled lens for optical components
Application: thick walled lens for LED headlamp
Material: PMMA
Hot runner system: 12 Hydraulic drops, Diamond Lux Line
In cooperation with: Engel, HRSflow, Innolite, Skymould
Special features: Total thickness of 22 mm, triple layer injection, overmoulding for high photometric quality. Initially, a preform is produced and further layers of the same material added to it in subsequent stages. Overmolding compensates for any sink marks in the surface of the previous layer and achieves high optical quality.
FLEXflow FAMILY: CHALLENGE YOUR EXPECTATIONS
Electric, efficient, evolved.
FLEXflow Family includes the electrically driven valve gate systems, FLEXflow and FLEXflow One.
How will you drive perfection?
The electrical technology is designed for the independent adjustment of each valve pin with precise control of stroke, velocity and force during opening and closing phases.
This solution assures accurate, easy to operate, flexible control of pressure and flow rates at each individual gate during the injection process.
Aesthetic benefits
- Quality improvements for Class “A” large, surfaces, chromed surfaces
- Warp reduction
- Optimal flow balancing
- Wall thickness reduction
Cost effective
- Clamping force reduction
- Scrap reduction
- High process repeatability
- Mold deflection reduction
- Successful family mold operation
Operational benefits
- Reduced maintenance
- Wider process window
- Clean operation
- Easy to use
HPgate: THE INNOVATIVE VALVE GATE SOLUTION

High-quality parts without flash
HPgate is the innovative solution suitable for direct injection on PMMA surfaces - as well as for reinforced materials - to optimize gate quality and avoid flashes.
Moreover, it simplifies the machining operations of the seat of the mold in the gate area allowing a high gate quality during the whole lifetime of the mold.
In order to obtain high quality parts characterized by an improved gate quality, HPgate technology integrates the conical and cylindrical solution, overcoming the limits of both configurations.
Benefits
- Improved gate quality compared to standard conical and cylindrical configurations
- Easier machining operations for the moldmaker
- Easy gate maintenance
- No puckering risks
- Wider process window and faster set-up operations
Main features
- The insert is screwed into the threaded seat machined into the mold
- Easily replaceable hard steel insert
- Conical – cylindrical valve gate
- Angle between surface normal and nozzle axis: MAX 5°
- Gate diameter: 2.0 – 2.5 – 3.0 mm
YOUR RELIABLE PARTNER FOR A WIDE RANGE OF APPLICATIONS
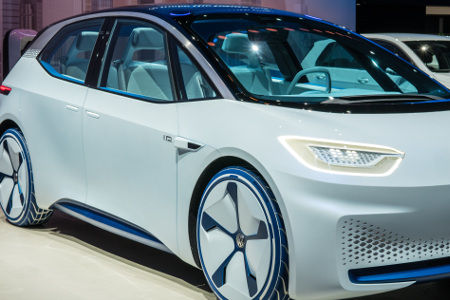
Automotive exterior
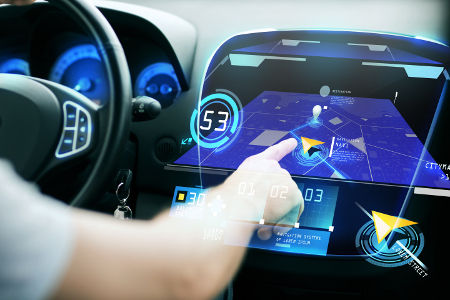
Automotive interior
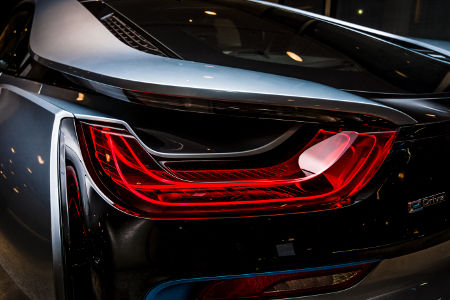
Automotive lighting
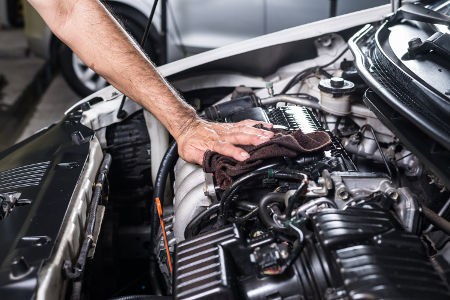
Under-the-hood
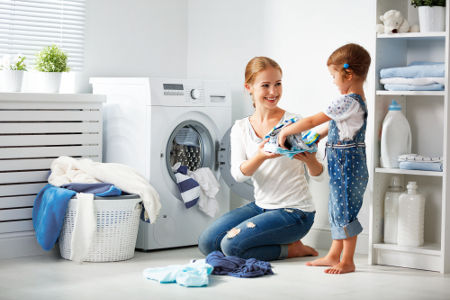
Domestic appliances
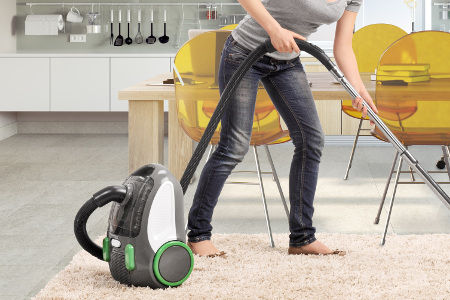
Houseware
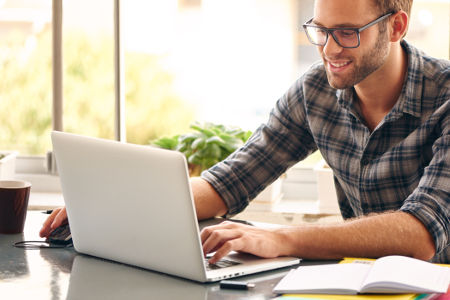
Technical applications
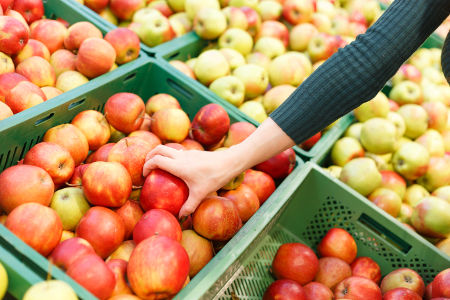
Logistics & Environmental
FOR ALL YOUR NEEDS, OUR EXCEPTIONAL SUPPORT
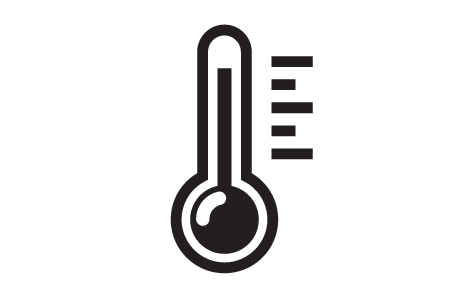
100% thermal analysis simulations
Specific thermal analysis simulations are provided on 100% of our systems in order to optimize final performance and to ensure a uniform thermal distribution.
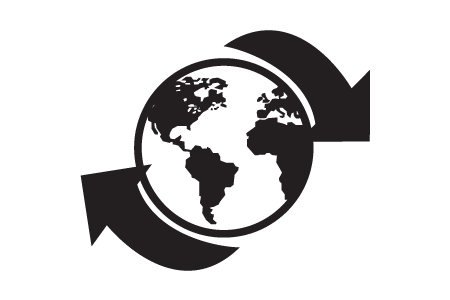
Identical world wide standard
Our processes, design, production and quality are identical wherever they are located: from our manufacturing facilities in Italy to Hangzhou-China, and Grand Rapids, Michigan USA.
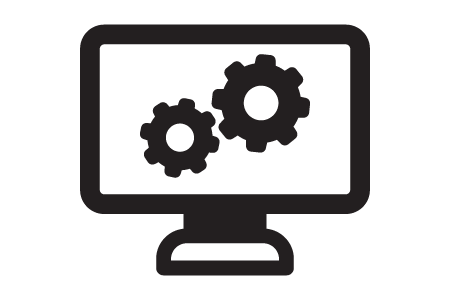
Our service 4.0: pre and after sales efficiency
We ensure a prompt response from our web-based service platform, optimized stocks of spare parts and our service tools such as Troubleshooting and e-TS (Electronic Tool Standard)
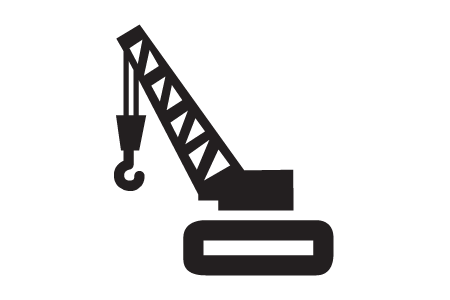
Automated production and process integration
We have invested significantly in the automation of the production of our products, not only increasing our capacity, but more importantly to ensure performance consistency and reliability.
Would you like to learn more about our hot runner solutions or meet us at MSV 2018?
We look forward to meeting you at Booth 20, Hall G1