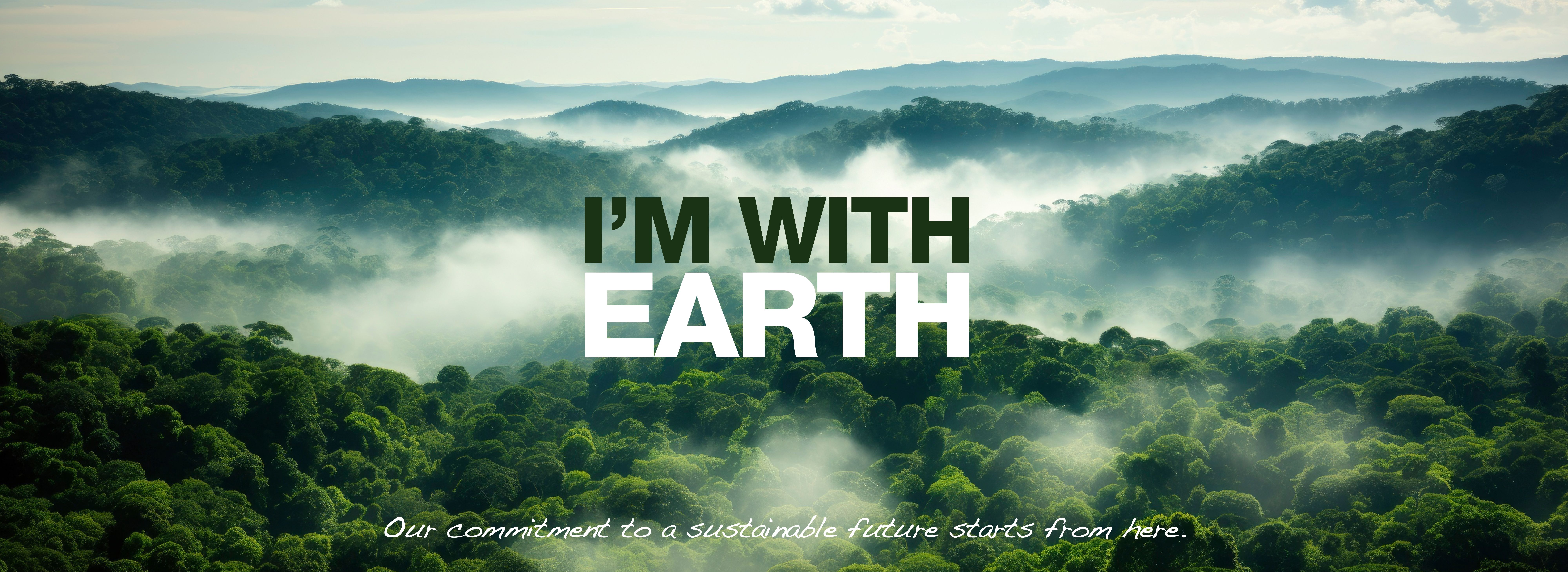
WE HAVE A PLAN
Following "Net-zero program" and "Circular Economy business model", we are putting into action a plan aimed to drastically reduce our carbon footprint and to enable the end users to make the injection process more sustainable.
START WITH CARBON FOOTPRINT CALCULATION
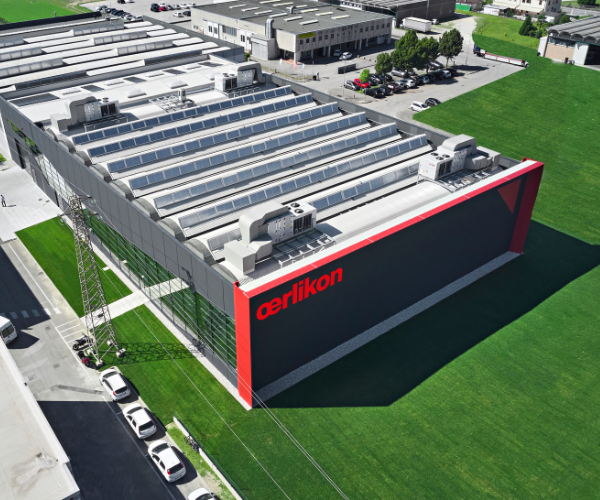
Our plan started with the quantification of the actual CO2 emissions in our manufacturing process (internal consumption) and during the use of our products by clients and molders.
-
Internal CO2 generation: we measured the CO2 emissions in the 3 facilities, (Italy, Usa, China), and by our vendors, to generate our output and then calculated an average CO2 emission by drop manufactured.
-
Product usage CO2 generation: we have calculated the CO2 average emissions generated by our hot runners in the injection process and created a specific CO2 calculator tool to support our customers in tracking the emissions produced by the systems working on their plants.
GOAL 1: INTERNAL CO2 REDUCTION
DEFINE A REALISTIC TARGET AND TANGIBLE STRATEGIES
TO REDUCE INTERNAL CO2 GENERATION FOR THE PERIOD 2024-2027
Target: a 50% CO2 emissions reduction by 2027
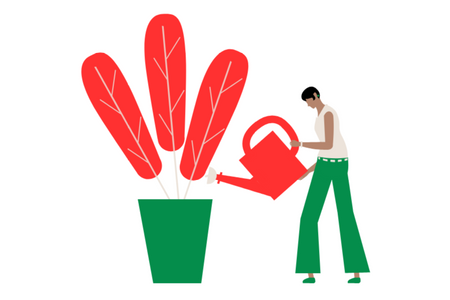
Photovoltaic electric power generation: we are increasing our internal green energy generation.
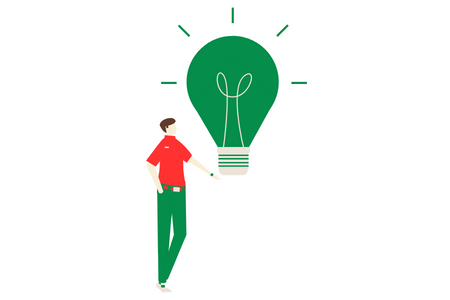
Green Electric Power: we are purchasing more green electric power from our suppliers.
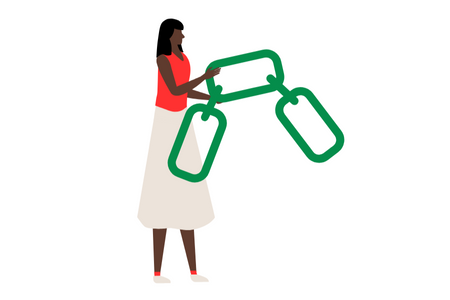
We are starting a Supplier certification process through “Ecovadis” to have a more sustainable supply chain.
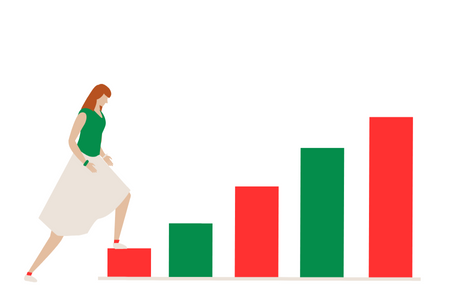
We are working on an Internal “Energy management system” aimed to measure and improve our processes.
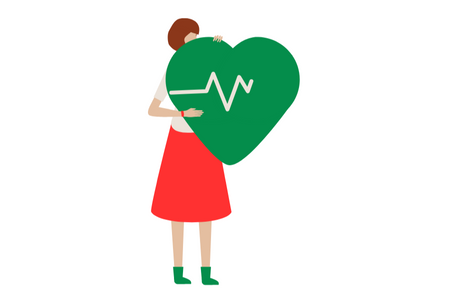
We are promoting activities to raise awareness about sustainability, among all employees .
GOAL 2: PRODUCT USAGE CO2 REDUCTION
ENABLE OUR END USERS TO MAKE THE INJECTION PROCESS MORE SUSTAINABLE
Target: injection process optimization
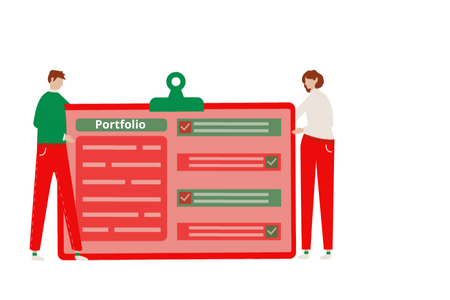
Product portfolio
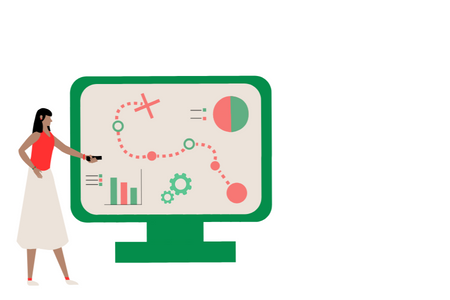
Process technology
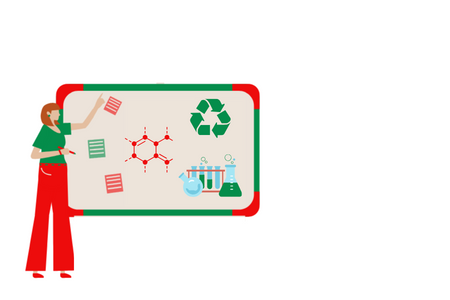
sustainable polymers
PRODUCT PORTFOLIO
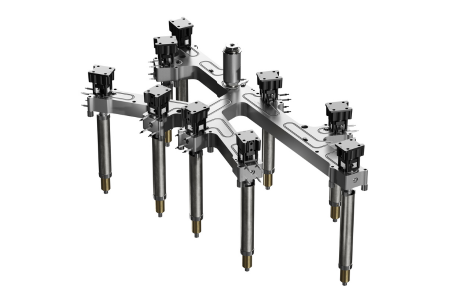
HRScool Evo
Actuators where water lines are not required:
- Optimal thermal insulation for energy saving
- No cooling equipment needed
- Reduction of the overall energy consumption (up to 10% per drop) according to the system dimension and the applications
- Thermal uniformity along the whole hot runner system
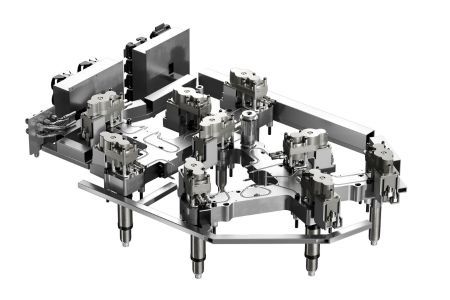
FLEXflow HRS
Servo driven valve gate for an accurate control of the process and energy/scraps savings:
- High quality part performance for Class“A” surfaces
- Wall thickness reduction
- Injection on film
- High process repeatability
- Family tools enabler
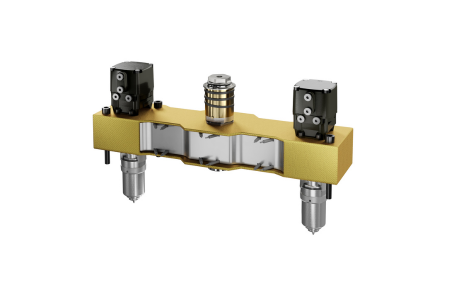
I-Shield HRS Insulating cover
Energy cost and carbon footprint reduction for End User:
- Time and energy reduction to warm up the hot runner system
- Less energy needed to keep the hot runner system at specific set point temperature
- Reduced energy consumption to condition the mould at a set point temperature
PROCESS TECHNOLOGY
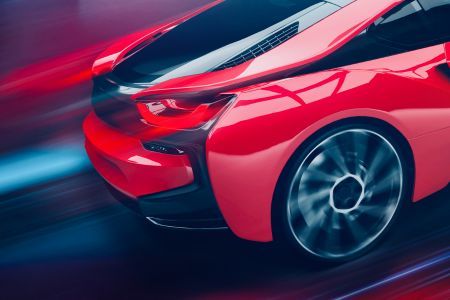
DIRECT INJECTION
HRS electrically driven hot runners ensure the production of "Class A" molding surfaces with no optically relevant defects on the injection point.

WARPAGE REDUCTION
Thanks to FLEXflow HRS technology, the packing pressure can be adjusted independently for each nozzle and part warpage can be significantly reduced. The overall result is “Class A” molding surface.
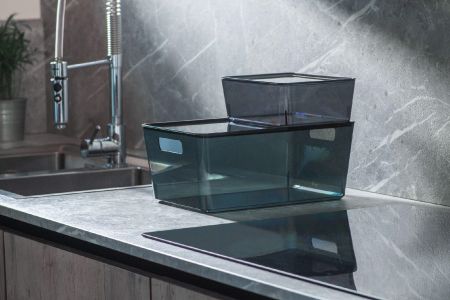
FAMILY TOOLS
HRS technology enables independent and precise adjustment of the filling rate for each cavity, even when parts differ considerably in dimension and volume. The precise control ensures the filling of all cavities simultaneously, preventing overfilling and flash issues.
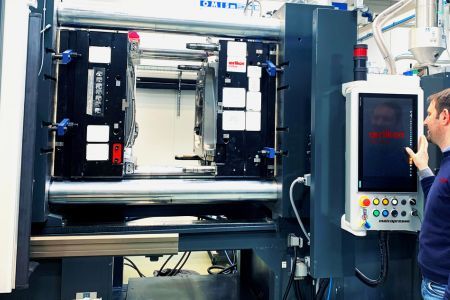
CLAMPING FORCE REDUCTION
HRS technology enables a larger process window and an optimal pressure distribution, resulting in an injection machine clamping force reduction by 20%.
SUSTAINABLE POLYMERS
Oerlikon HRSflow has tested and developed specific technical solutions for biopolymers and PCR resins injection, given the narrow process window of these polymers and their thermal/shear sensitivities. Our systems are conceived to prevent damages caused by external particles accidentally present in the bio or PCR compounds, to avoid any streaking or flow marks that could affect the cosmetic and functional result of the part.
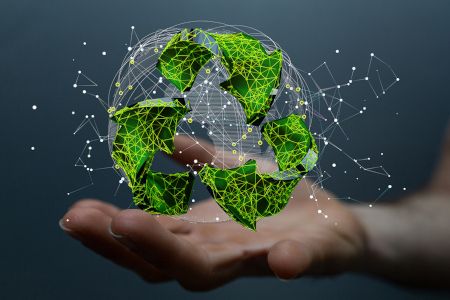
PCR Compounds processability
- Dedicated hot runner system configurations and applications
- BALINIT® MOLDENA coating by Oerlikon Balzers to optimize flow behaviour
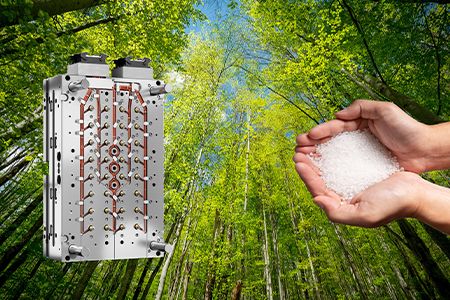
Biopolymer processability
- Dedicated technical solution to cope with polymers behaviours
- Shear sensitivity